Industrial pumps are essential in industries ranging from oil and gas to wastewater management and manufacturing. These powerful machines move liquids, chemicals, and even solid-laden slurries, often working tirelessly in extreme conditions. However, their constant use and exposure to harsh substances make them vulnerable to wear and tear, where industrial pump repair becomes crucial.
Neglecting industrial pump repair can lead to costly downtime, inefficient operations, and potentially catastrophic failures. A well-maintained pump keeps processes running smoothly, so repair services are more than just maintenance—they’re a lifeline for industries. This blog delves into the importance of industrial pump repair when to consider it, and how it can save costs and prevent downtime.
The High Cost of Industrial Pump Failure
Industrial pumps don’t just quit without warning; they gradually decline, affecting overall performance. Pump failure signs include decreased flow rates, rising energy consumption, unusual vibrations, and leaking seals. These early indicators are critical for proactive maintenance, as the costs of unplanned pump failure can be staggering.
According to a survey by the Aberdeen Group, unplanned downtime can cost companies anywhere from $250,000 to $500,000 per hour. 82% of companies experienced unplanned downtime in the past three years, with mechanical failure as one of the primary causes. Pumps, critical to the continuity of various processes, are often at the center of these costly disruptions.
Why Industrial Pump Repair Is Essential for Efficiency
The importance of industrial pump repair isn’t limited to preventing downtime; it also enhances operational efficiency. Studies have shown that a well-maintained pump can save up to 20-30% of energy. Since industrial pumps account for nearly 20% of the world’s electrical energy consumption, improving efficiency offers substantial financial and environmental benefits. For example, the U.S. Department of Energy has highlighted that energy costs comprise nearly 90% of a pump’s total lifetime cost. Companies can significantly reduce these expenses by addressing inefficiencies through timely repair and maintenance.
SPump Needs Repair
Recognizing when a pump needs repair can prevent it from reaching the point of failure. Here are some red flags to watch for:
Drop in Performance: Reduced flow rates and pressure indicate that the pump isn’t operating at its best and likely requires repair.
Unusual Sounds or Vibrations: Industrial pumps are built to handle tough conditions but should still operate smoothly. Increased noise and vibration can indicate bearings, impellers, or shaft alignment issues.
Temperature Increases: Excessive heat may signal friction or wear in the pump’s moving parts, suggesting the need for immediate repair.
Leaks and Seal Failures: Leaks often mean that seals or gaskets are compromised, which can lead to contamination or further damage.
Increased Power Consumption: An inefficient pump tends to draw more power, so a sudden spike in energy costs could mean your pump needs an overhaul.
The Process of Industrial Pump Repair
Industrial pump repair isn’t a one-size-fits-all service; it involves a thorough examination and specific interventions tailored to each pump’s unique issues. Here’s a look at a typical repair process:
Inspection and Diagnosis: The first step is a comprehensive inspection to diagnose the exact issue. Technicians check components like bearings, seals, and rotors, looking for wear or damage.
Disassembly and Cleaning: The pump is disassembled once the problem areas are identified. Each component is cleaned to remove build-up and debris that could impede its performance.
Replacement of Worn Parts: Worn-out components are either repaired or replaced depending on their condition. This may include impellers, seals, or gaskets—anything essential to the pump’s function.
Reassembly and Testing: After replacing damaged parts, the pump is reassembled and tested rigorously to ensure it meets operational standards. Testing includes pressure tests, flow checks, and performance calibration to confirm the pump is in top shape.
Reinstallation and Calibration: The final step is returning the pump to its operational setting. Calibration ensures the pump meets specific parameters, minimizing issues once it’s back in service.
Benefits of Proactive Pump Repair and Maintenance
Proactive maintenance and repair schedules can drastically reduce the likelihood of unplanned pump failures. These practices also significantly impact a company’s bottom line, boosting productivity and reducing long-term costs. Proactive industrial pump repair has been shown to reduce overall maintenance costs by 10-15% and can extend a pump’s operational life by up to 50%.
Minimized Downtime: Addressing minor issues early on prevents them from escalating into costly breakdowns. This proactive approach keeps production lines moving seamlessly, helping companies avoid lengthy downtimes and meet their production targets more reliably.
Enhanced Energy Efficiency: Inefficient pumps consume more power than necessary. Companies can improve pump efficiency by repairing and optimizing critical components like impellers and seals, resulting in significant energy savings over time.
Cost-Effective Solution: Investing in industrial pump maintenance increases operational effectiveness and durability. Regular maintenance is a wise financial choice, resulting in significant savings from lower energy costs and fewer emergency repairs.
Enhanced Safety: Industries handling flammable, corrosive, or hazardous products are especially vulnerable to the dangers posed by malfunctioning pumps. Regular maintenance reduces the possibility of leaks, explosions, and other safety hazards, making the workplace safer.
Technology’s Role in Industrial Pump Repair
Innovations in technology have transformed industrial pump repair. Today, predictive maintenance systems use Internet of Things (IoT) sensors to monitor pump performance, tracking factors like vibration, temperature, and energy consumption. This allows companies to schedule repairs precisely when needed, maximizing uptime and reducing repair costs.
Another exciting development is computer-based diagnostics and AI-driven analytics, which enable more accurate assessments of a pump’s health. A pump equipped with these technologies can alert operators to potential problems long before they affect performance, revolutionizing how industrial pump repair is approached.
Case Study: How One Facility Saved Big with Industrial Pump Repair
Consider the example of a large chemical processing plant facing frequent pump failures due to inadequate maintenance. By implementing a proactive repair program and using IoT sensors to monitor pump health, the plant cut its annual pump-related downtime by 40% and reduced repair costs by $500,000 annually. This kept the plant operating smoothly and boosted profitability, demonstrating the massive impact of industrial pump repair on an industrial scale.
Conclusion
Industrial pump repair is not just a maintenance task—it’s a critical service that keeps industries running. The benefits extend beyond avoiding downtime, improving efficiency, lowering energy costs, and enhancing safety. As technology advances, industrial pump repair approaches become increasingly proactive, helping facilities of all kinds stay productive and competitive.
Understanding the importance of industrial pump repair empowers companies to prioritize this vital service. Whether through predictive maintenance, advanced diagnostics, or well-timed repairs, keeping pumps in peak condition keeps the industry’s heart beating.
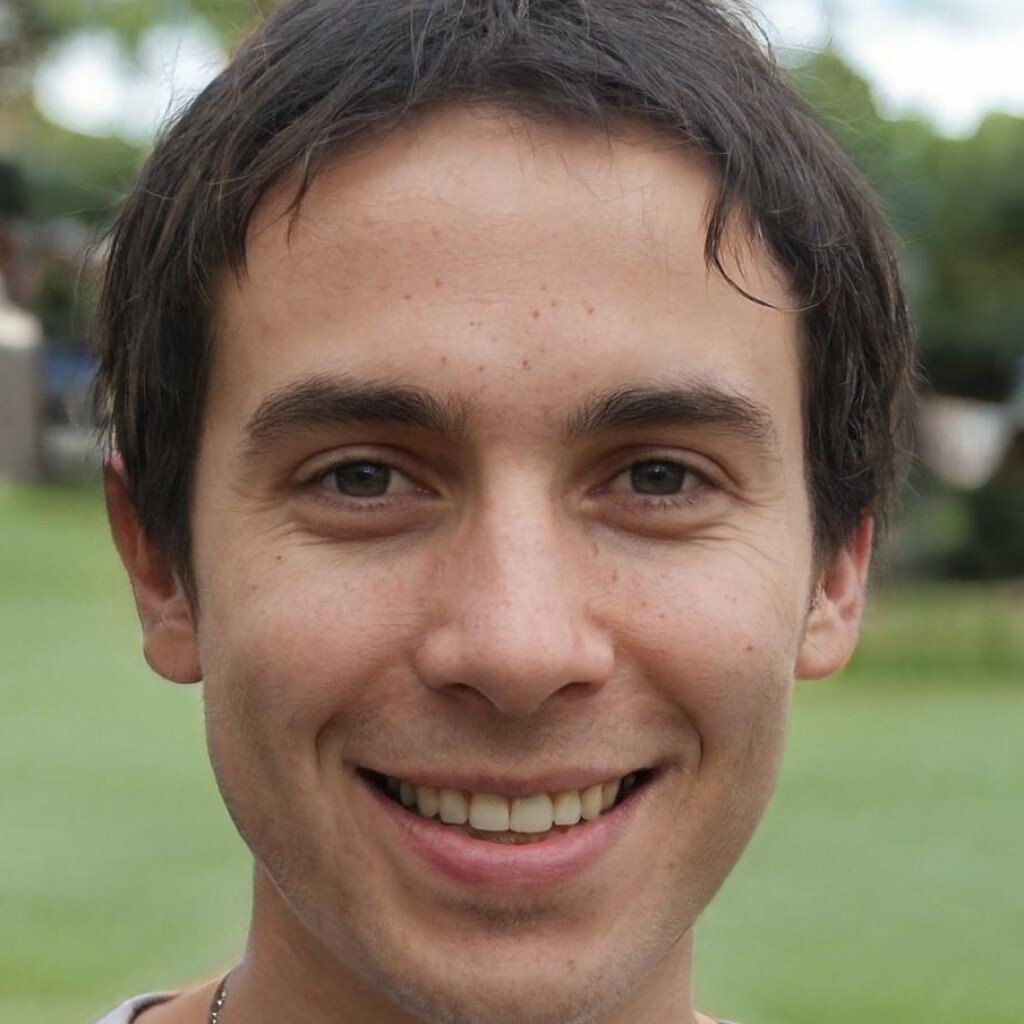
Hiking addict, ramen eater, music blogger, Swiss design-head and screen printer. Operating at the fulcrum of design and function to craft meaningful ideas that endure. Check me out on Dribbble or Medium.